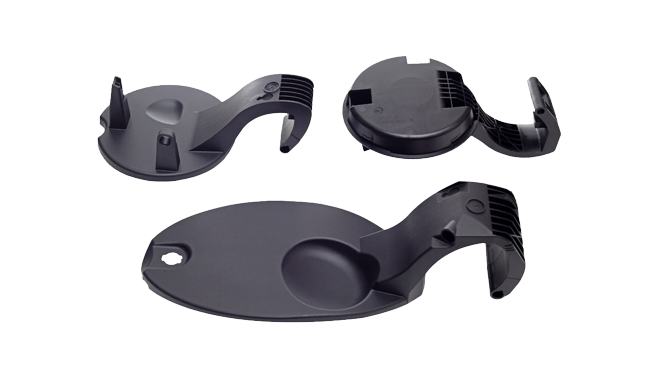
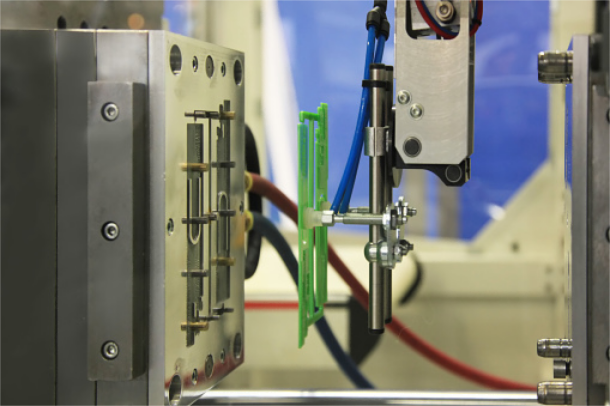
Injection mold
Injection molding is a manufacturing process in which a thermoplastic material is melted and injected into a mold cavity.
From small parts to large items such as automobile parts and storage containers. Injection molding is a highly efficient and precise process that can be used to create complex shapes and designs with minimal waste or error.
Available Injection Molding materials
Plastic material
1. ABS (Acrylonitrile Butadiene Styrene)
2. PE (Polyethylene)
3. PP (Polypropylene)
4. PC (Polycarbonate)
5. Nylon
6. POM (Acetal)
7. PEEK (Polyether Ether Ketone)
8. PET (Polyethylene Terephthalate)
9. TPE (Thermoplastic Elastomer)
10. PMMA (Polymethyl Methacrylate)
Rubber material
1. Silicone Rubber
2. Ethylene Propylene Diene Monomer (EPDM) Rubber
3. Neoprene Rubber
4. Butyl Rubber
5. Natural Rubber
6. Polyurethane Rubber (PU)
7. Styrene-Butadiene Rubber (SBR)
8. Fluoroelastomer Rubber (FKM)
9. Nitrile Rubber (NBR)
10. Hypalon Rubber
Upload your part
More info
What's the advantage of injection molding
1. High production efficiency: Injection molding allows for fast production of large quantities of parts, making it ideal for mass production.
2. Consistency and precision: With injection molding, the exact shape and dimensions of the part can be consistently replicated with high precision, ensuring uniformity and accuracy in every part produced.
3. Versatility: Injection molding can create complex shapes and intricate designs with a high degree of accuracy, making it ideal for producing components and parts for a wide range of applications.
4. Cost-effective: Injection molding is a cost-effective option for high-volume production runs, as it requires minimal labor and tooling costs, resulting in lower overall costs per part.
5. Reduced waste: Injection molding allows for precise control over material usage, resulting in minimal waste and lower costs.
6. High-quality finishes: Injection molding can produce parts with high-quality finishes and surface textures, requiring little to no finishing work.
Injection molding Applications
There are numerous injection molding applications across various industries. Here are some of the most common:
1. Automotive industry: Injection molding is used to produce various automotive parts such as bumpers, dashboards, interior trims, and wheels.
2. Medical industry: Injection molding is used to produce medical devices such as syringes, IV tubes, surgical instruments, and implantable devices.
3. Electronics industry: Injection molding is used to produce electronic components such as connectors, switch covers, and housing for electronic devices.
4. Packaging industry: Injection molding is used to produce packaging containers such as bottles, jars, and lids.
5. Consumer goods industry: Injection molding is used to produce a range of consumer goods such as toys, kitchenware, and furniture components.
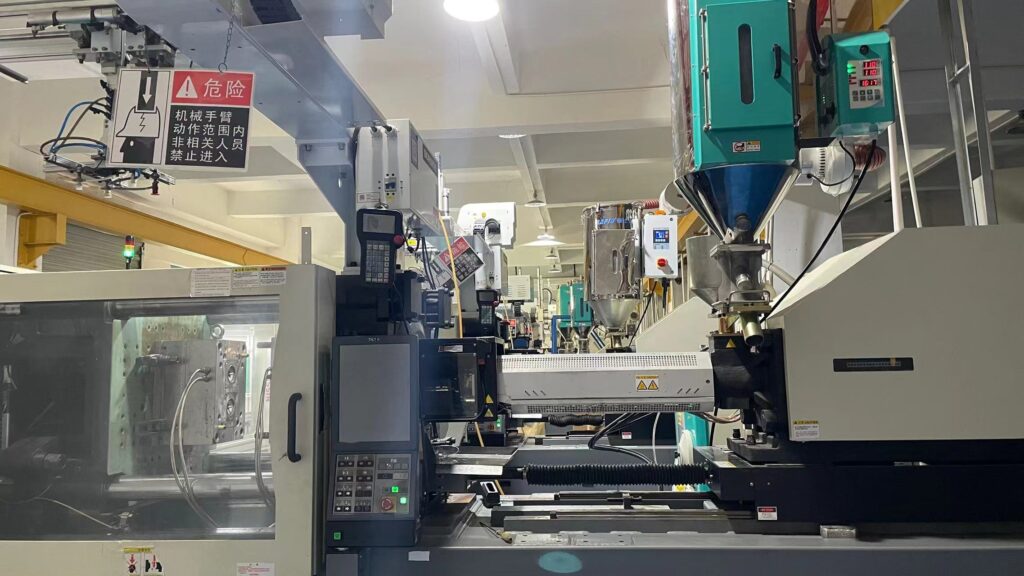